I just uploaded a video here about Spiral Phyllotaxis patterns in OpenSCAD. The video, originally posted by me on YouTube some years ago, is about a script that I made to demonstrate Spiral Phyllotaxis. Phyllotaxis is a term used for patterns that emerge during the growth of plants. Spiral Phyllotaxis is observed in the heads […]
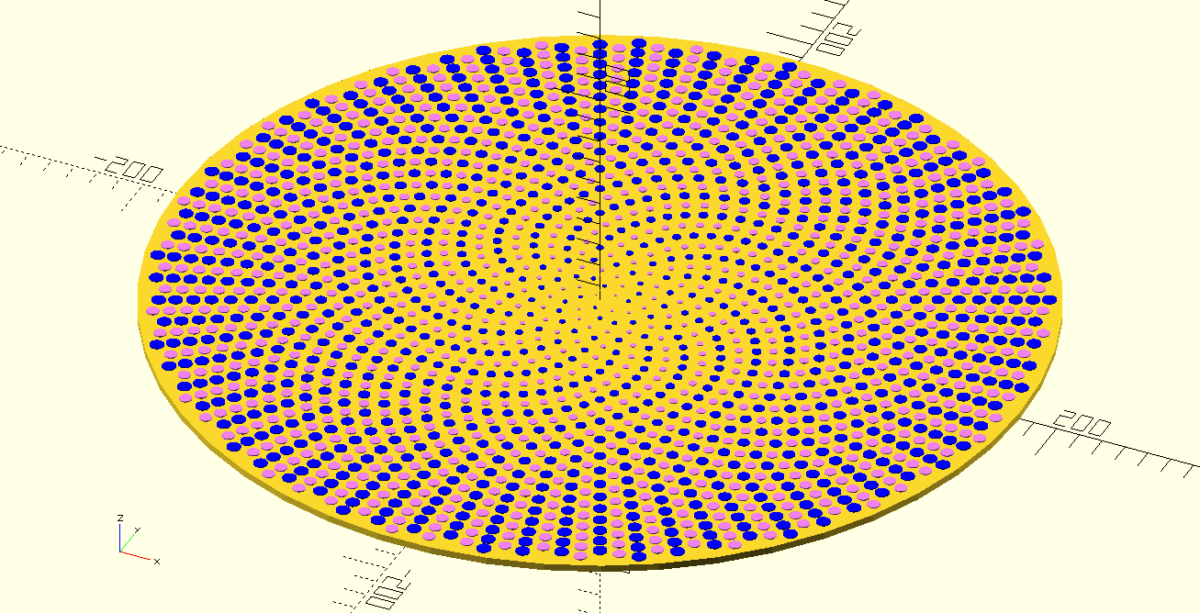